Which surface treatment to choose?
Unlike ordinary ferrite magnets, all neodymium magnets must be covered with a layer of protective material. The NdFeB material reacts with oxygen in the air and the bare magnet would gradually chemically decompose (rust).
With nickel, gold, zinc, chrome and epoxy resin surfaces, the strength of the magnet is the same, because the protective layer is usually too thin to affect the strength. The layer of rubber or plastic tends to be thicker and therefore partially reduces the strength of the magnet (increases the distance between the attracted object and the magnet).
There are several options for finishing neodymium magnets. In our e-shop with magnets we mainly offer nickel-plated magnets, but in our offer you can also find several magnets with a surface treatment of gold, polyepoxide or rubber-coated magnets.
A brief comparison
surface | scratch resistance | moisture resistance | impact resistance | price |
---|---|---|---|---|
nickel (Ni-Cu-Ni) | good | good | good | the lowest |
zinc (Zn) | very good | very good | good | low |
chromium (Ni-Cu-Ni-Cr) | very good | good | good | low |
gold (Ni-Cu-Ni-Au) | below average | excellent | good | high |
polyepoxide (Ni-Cu-Ni-epoxide) | bad | excellent | good | average |
rubber | excellent | excellent | excellent | average |
plastic | excellent | excellent | excellent | average |
Nickel
- there are actually three layers: nickel-copper-nickel
- the most common surface treatment, most of our magnets are nickel plated
- a combination of good features and the lowest price
- thickness: 10-15 micrometres
- colour: silver

Zinc
- a simple layer of zinc metal
- slightly better resistance to scratches and moisture, especially to salt water
- thickness: 8-10 micrometres
- colour: grey-blue
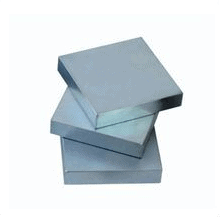
Chromium
- four layers: nickel-copper-nickel-chromium
- compared to nickel and zinc, better scratch resistance, therefore we recommend chrome for ball magnets (with balls, all the force is concentrated at one point of contact)
- thickness: 12-17 micrometres
- colour: dark shiny metal
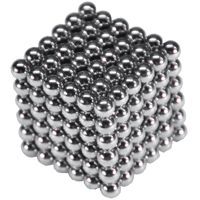
Epoxy resin (polyepoxide)
- four layers: nickel-copper-nickel-epoxy
- excellent resistance to moisture (including salt water) and other chemicals
- you must exercise caution because the layer of polyepoxide can be easily scratched with a sharp object, the chemical resistance of the magnet is then lost and in the scratched place it starts to behave like a normal nickel treatment (all our magnets still have a standard nickel protective layer under the polyepoxide)
- thickness: 20-40 micrometres
- colour: matte, black
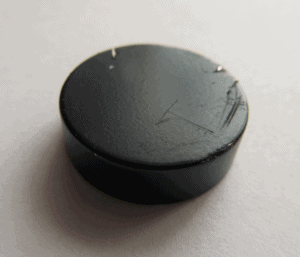
Gold
- four layers: nickel-copper-nickel-gold
- a very thin layer of pure 24-carat gold is applied to the standard layer of nickel
- excellent resistance to moisture (including salt water) and other chemicals
- the layer of gold can rub off if it is regularly exposed to friction (but it is still much more durable than epoxy resin)
- suitable for applications where the appearance of the magnets is important, the gold finish is aesthetically appealing
- thickness: 10-15 micrometres handy helpers Ni-Cu-Ni; 0.05 micrometre gold
- colour: gold
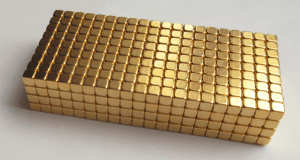
Rubber
- nickel-rubber or sometimes just rubber
- very good impact resistance, rubber absorbs impact energy
- rubber has a high coefficient of friction: it is difficult to slide along any surface, it stays in place
- good chemical resistance
- the magnet is somewhat weaker, because the thicker layer of rubber increases the distance between the magnet and the attracted object
- thickness: 0.5 to 2 millimetres
- colour: mostly black
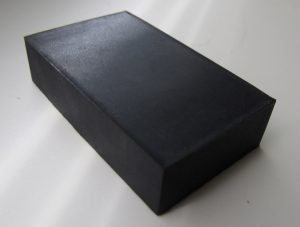
Plastic
- nickel-plastic or sometimes just plastic
- like rubber, very good impact resistance
- unlike rubber, there is less friction between plastic and other surfaces
- good chemical resistance
- the layer of plastic increases the distance between the magnet and the attracted object and thus slightly reduces the strength of the magnet
- thickness: 0.5 to 2 millimetres
- colour: various
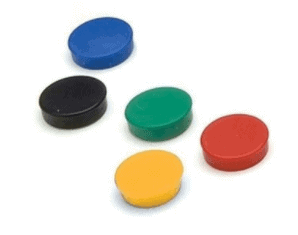
In this video, you can see the difference in the impact resistance of magnets covered with plastic and nickel:
Custom-made magnets
If you need magnets with a special surface treatment, you can describe your requirements on the Magnet production page. You can also contact us at info@orodian.com or call +421 940 640 600.